“This is one of the best organizations I have audited for its size”
– ISO auditor Mike Meketa
Our shop utilizes CNC Lathes and CNC Machining Centers. The lathes are capable of turning, boring, grooving, threading and facing, etc. We have Auto Loading Lathes to handle the high volume jobs.
The Machining Centers have 18 x 12 inch of travel and are capable of Milling, Slotting, Drilling, Tapping, Re-Tapping, Boring, etc. Some Machining Centers have dual pallets that enable us to machine two (2) or more sides of a part with just one (1) set-up. This gives our Customers a better turn around time on their parts. Partials can be shipped without having to wait for the entire order to be completed.
We also have Drilling and Tapping Machines with right-hand, left-hand and re-tapping capabilities.
And our Linear Abrasive Grinder for one sided grinding for high production jobs.
Grinding
Our grinding machines are production oriented and can run parts up to 5.5 inches in diameter. The parts are fed on a conveyor through the machine and must be magnetic to be held to the belt for grinding. This is a one-side grinding operation.
These machines can also be used for a roughing operation before a fine grinding operation to save on fine grinding costs.
Depending on the parts these machines can hold flatness of .0004, finish of less than RA20, and overall thickness of .0015.
The machines are set up in cells for parts to be ground, brush deburred, dipped in RP if needed, and packed per customer specifications.

Turning
Turning is the process of shaping a part by rotating it and moving a cutting tool along its surface. The cutting tool removes material from the part and creates a cylindrical shape. Turning can be done manually or with a computer-controlled machine and can produce external and internal features, such as slots, tapers, and threads.
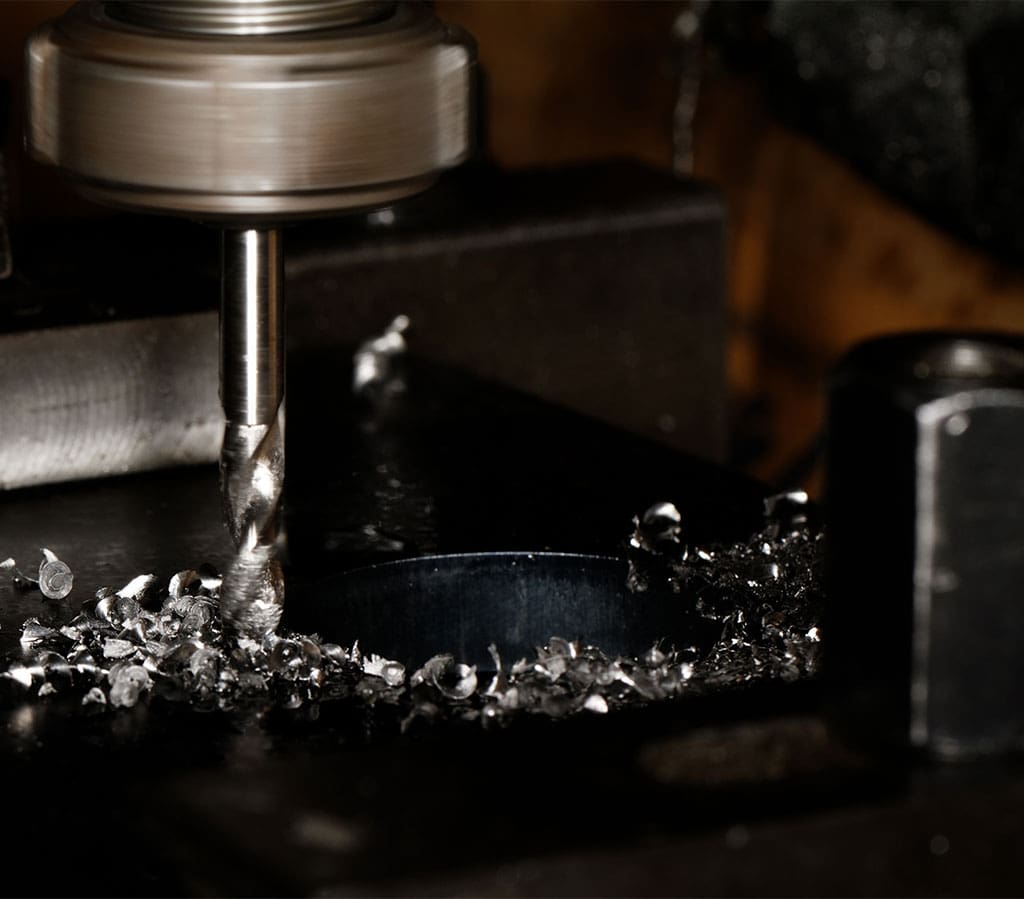
Boring
Boring enlarges a hole that has already been drilled or cast by using a single-point cutting tool or a boring head with multiple cutting tools. Boring can improve the size, shape, and surface finish of the hole, as well as make it concentric with the outer diameter of the part.
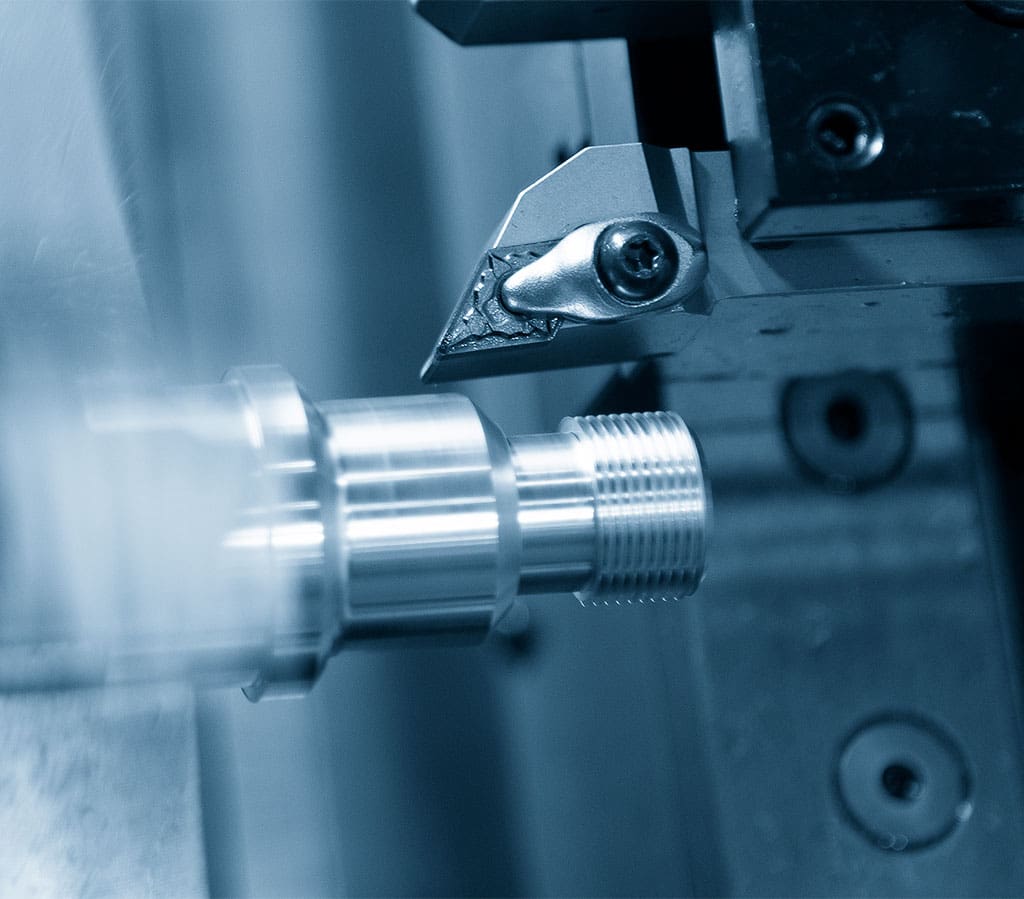
Grooving
Grooving cuts a narrow cavity or recess on the surface of a part, usually with a single-point cutting tool or a boring head. Grooving can be done on external, internal, or face surfaces of cylindrical or conical parts. Grooving can create different shapes and sizes of grooves, such as slots, tapers, and threads. Grooving is often used to ensure the correct fit for mating parts or to improve the appearance or function of a part.
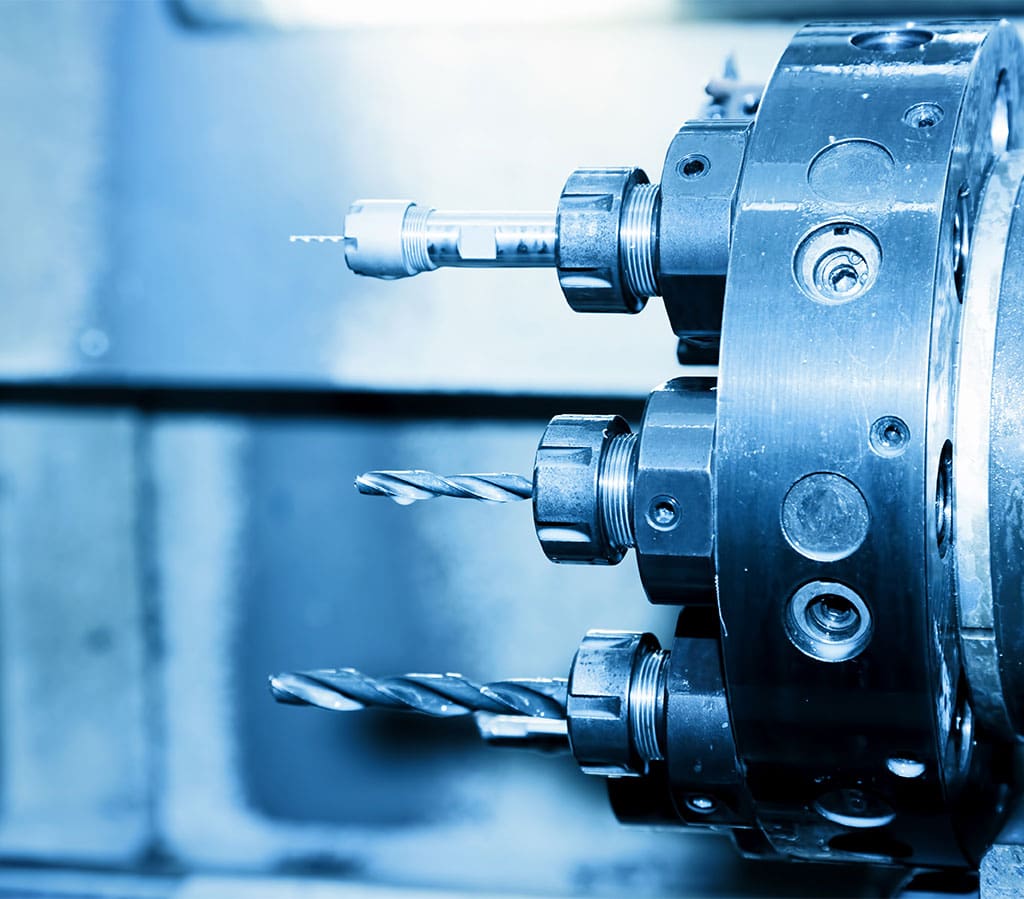
Threading
Threading creates a screw thread on a part by using a cutting tool or a forming tool. A screw thread is a helical groove that allows two parts to be joined together or to transmit power or motion. Threading can be done by various methods, such as thread turning, thread milling, thread cutting, thread rolling, and thread forming. Each method has its own advantages and disadvantages depending on the type, size, pitch, and quality of the thread required.

Facing
Facing removes material from the end and/or shoulder of a part, using a special tool to produce a smooth surface perpendicular to the rotational axis of the part. Facing can be done on a lathe or a milling machine, depending on the type and shape of the part. Facing on a lathe uses a facing tool to cut a flat surface perpendicular to the workpiece’s rotational axis as it spins in the chuck. Facing on a milling machine uses a face mill, shell mill, or fly cutter to cut a flat surface perpendicular to the axes of the milling cutter as the table feeds the part across the cutter. Facing is often used to reduce the length of the part, improve its surface finish, or create mating surfaces for other parts.

Milling
Milling is the process of removing material from a part by using rotating cutters that move along its surface. Cutters can have different shapes, sizes, and numbers of teeth, depending on the desired outcome. Milling can produce a variety of features and finishes on the part, such as slots, holes, curves, and planes. Milling can be done on vertical or horizontal milling machines, CNC machines, or multitasking machines.
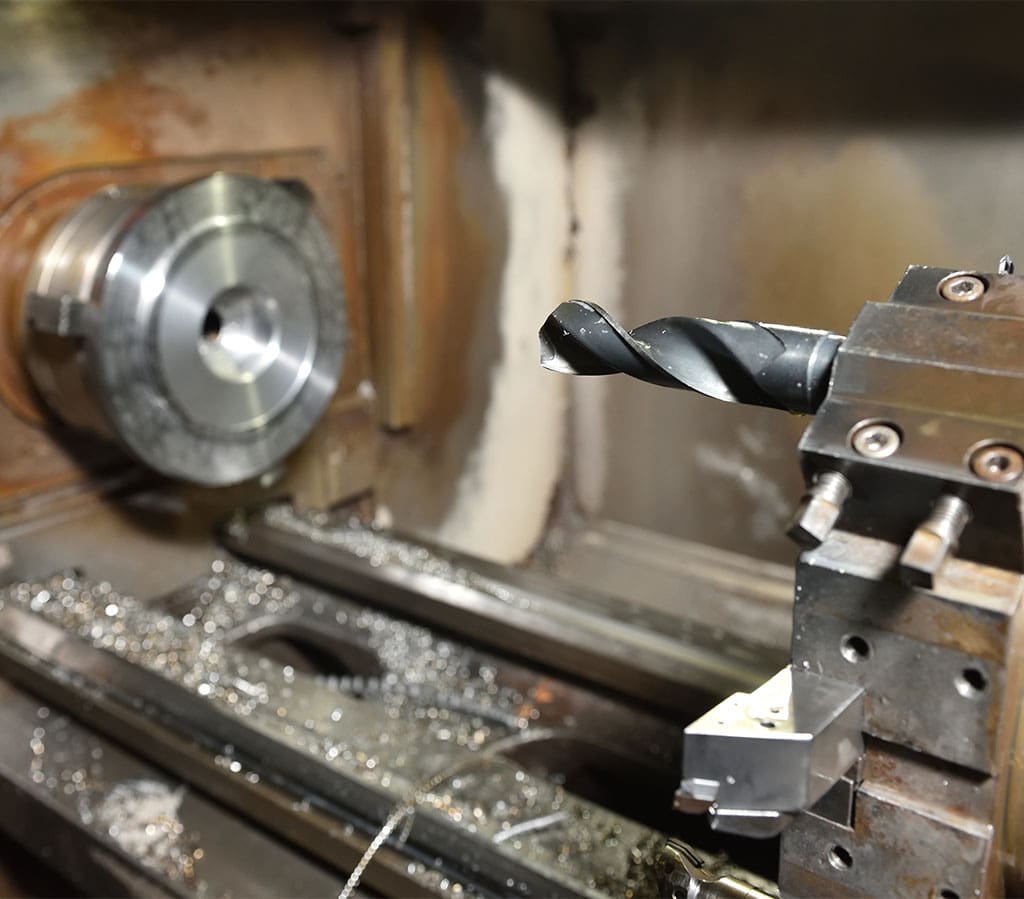
Slotting
Slotting is the process of cutting a narrow cavity or recess on the surface of a part, usually with a single-point cutting tool or a boring head. Slotting can be done on external, internal, or face surfaces of cylindrical or conical parts. Slotting can create different shapes and sizes of grooves, such as slots, tapers, and threads. Slotting is often used to ensure the correct fit for mating parts, or to improve the appearance or function of a part.
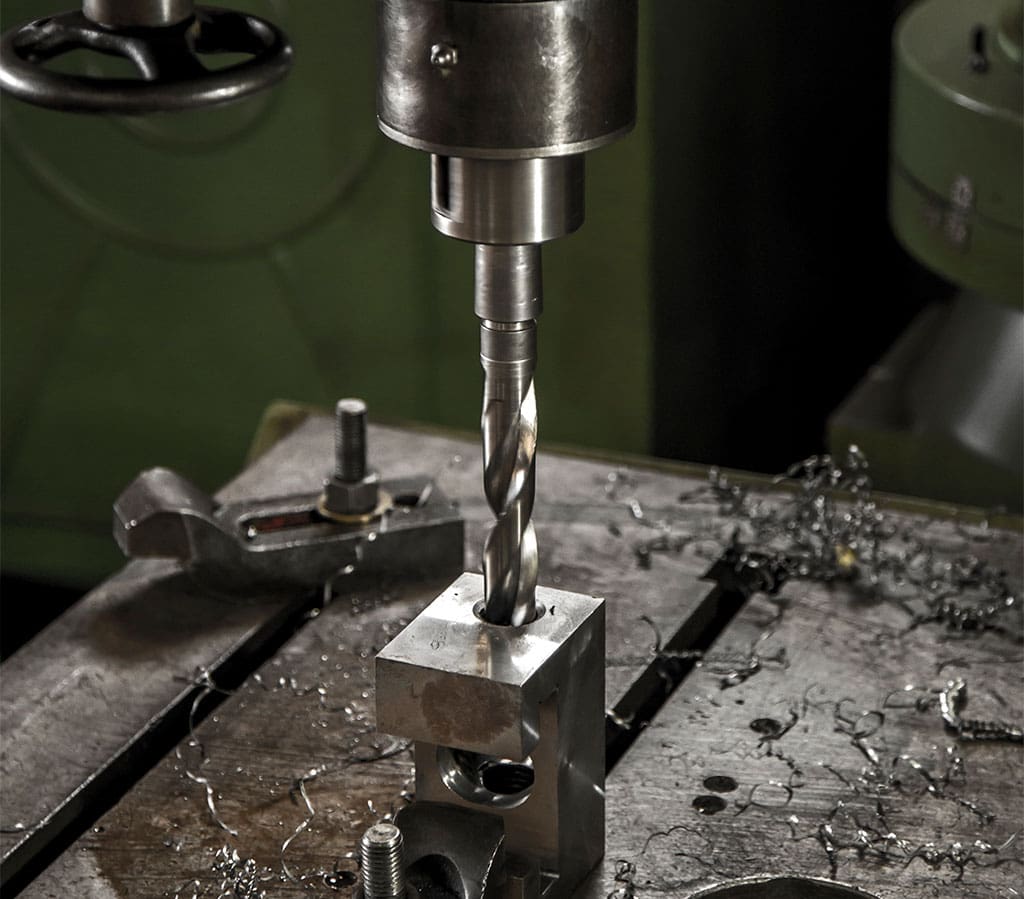
Drilling
Drilling can be done on our various lathes, milling machines, or drill presses. Drilling can produce holes with different diameters, depths, and shapes.
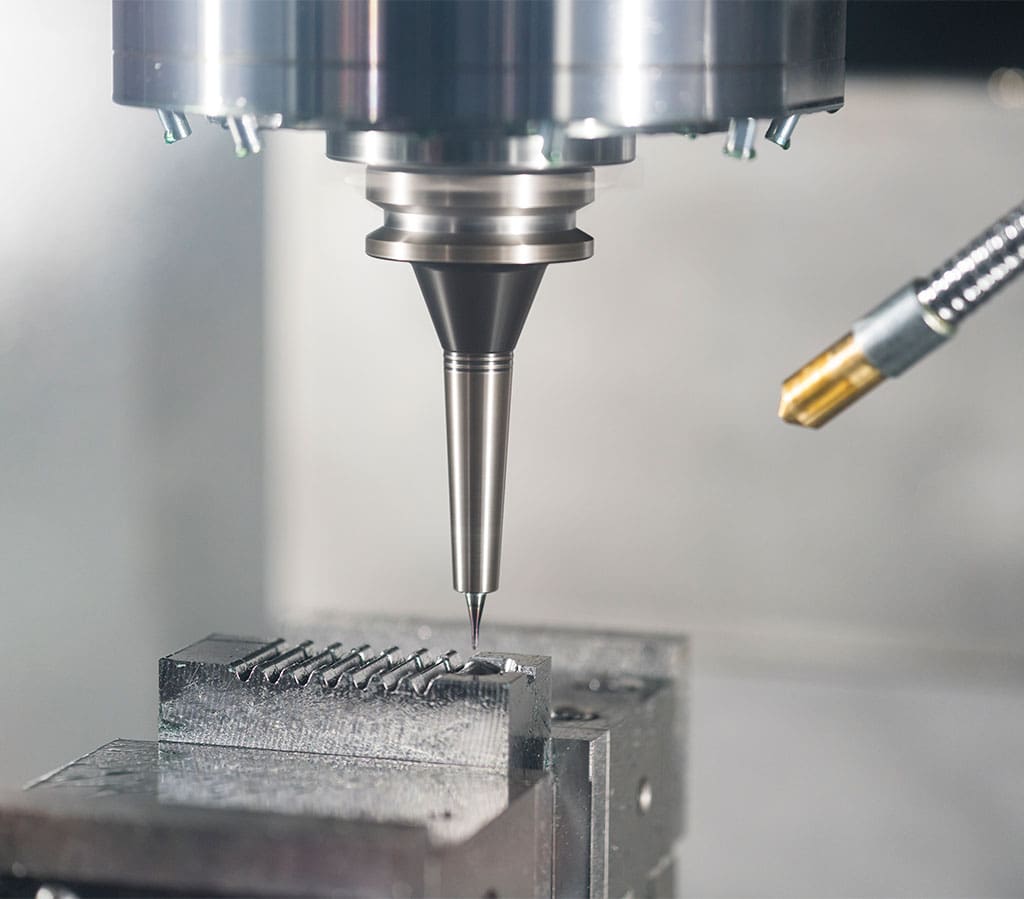
Tapping
Tapping cuts a thread inside a hole so that a cap screw or bolt can be threaded into the hole. Tapping can be done on our various machines, such as lathes, milling machines, or drill presses. Tapping can be performed by using either a cutting tap or a forming tap.
Join Our Team
Looking for a challenging and rewarding career in the machining industry? Established in 1995, Accu-Chek Machining Inc., is the leading secondary machining company based in St Marys, PA. We are always looking for talented individuals to join our team.
We offer competitive wages and benefits, as well as opportunities for training and advancement.